Wie werden 3D Druck Bauteile kalkuliert?
Wir geben Ihnen einen Einblick in unsere Kalkulation
Der 3D Druck stellt die wohl schnellste und billigste Methode dar, Prototypen beziehungsweise Unikate herzustellen. Durch die Entwicklungen der letzten Jahre lohnt es sich auch Kleinserien additiv herzustellen. Durch den erhöhten Bedarf an 3D gedruckten Bauteilen und dem mittlerweile vielfältigen Angebot des Marktes wird es immer wichtiger zu verstehen, wie sich die Preise für ein oder mehrere Bauteile zusammensetzen.
Dieser Artikel soll einen Einblick in die Preisgestaltung bei 3DBAVARIA geben und unseren Kunden transparent darlegen, welche Faktoren wir bei der Preisfindung mit einbeziehen. Mit Hilfe des Artikels „3D Druck Kosten verringern“, können zudem Schritte abgeleitet werden, welche die Kosten noch vor der Erstellung einer Anfrage positiv beeinflussen.
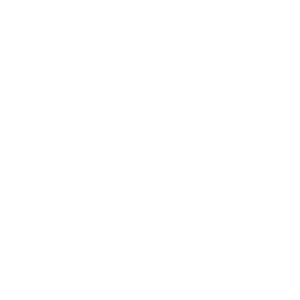
Unsere Kalkulationsmethoden
Bauteilvolumen
Mit Bauteilvolumen ist das solide Materialvolumen eines Bauteils gemeint. Um daraus einen Preis für das 3D Druck Teil zu kalkulieren, wird dieses Volumen mit einem festen Preis pro cm³ multipliziert. In diesem Kubikzentimeterpreis sind alle Einflussfaktoren, welche Sie im weiteren Verlauf dieser Seite nachlesen können, abgebildet. Diese Methode der Preisfindung verwenden wir für folgende Verfahren:
- Selektives Lasersintern (SLS)
- HP Multi Jet Fusion (HP MJF)
- Schmelzschichtung (FDM/FFF)
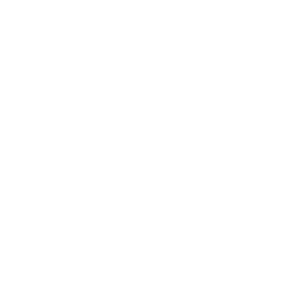
Bounding Box
Die sog. Bounding Box beschreibt den kleinsten Quader, in welchem Ihr Bauteil Platz findet. Auch bei dieser Methode wird unter Betrachtung aller möglichen Einflussfaktoren (s.u.) ein Preis pro cm³ Bounding Box ermittelt, welcher dann mit dem entsprechenden Volumen dieser Box multipliziert wird.
Diese Methode der Preisfindung verwenden wir für folgende Verfahren:
- Selektives Lasersintern (SLS)
Die SLS Technologie lässt technologisch beide Möglichkeiten der genannten Kalkulationsmethoden zu. Die sich daraus ergebenden zum Teil erheblichen Preisunterschiede sind meist nicht gerechtfertigt. Unser Online 3D Druck Kalkulator entscheiden deshalb automatisch, welche Methode für Ihr Bauteil die günstigere ist.
Welche Faktoren fließen in die Kalkulation mit ein?
Grundsätzlich unterscheiden sich die Preiskalkulationen jeder Technologien, da diese sich auch im Fertigungsprozess wesentlich unterscheiden. Bspw. sind bei pulverbettbasierte Verfahren (SLS oder HP MJF) im Gegensatz zum FDM Verfahren keine Stützstrukturen notwendig, die im Anschluss und teilweise sehr aufwendig entfernt werden müssen. Dennoch gibt es Faktoren, welche in jeder Technologie grundlegend für die Preisbildung sind:
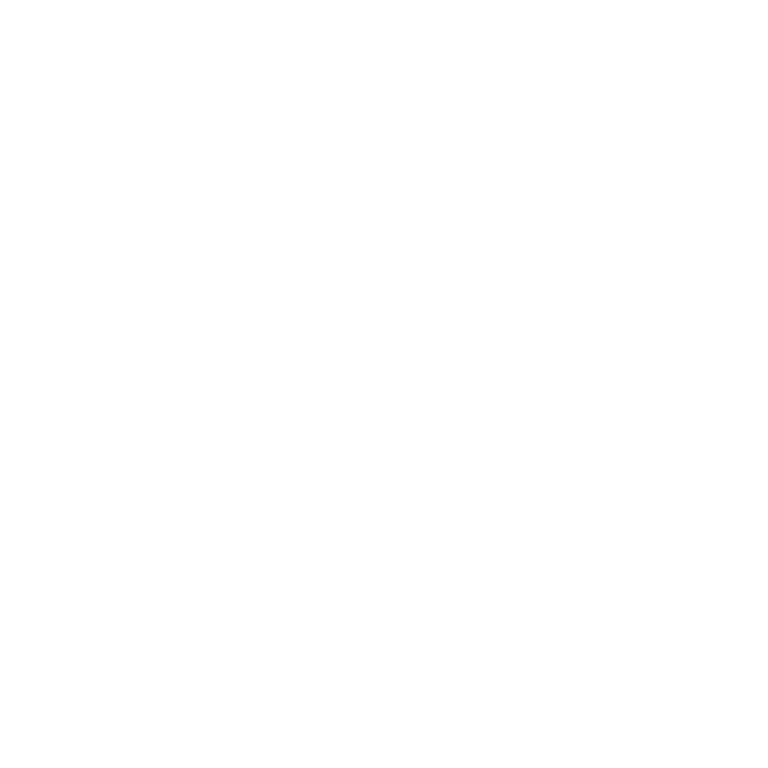
Verbrauchtes Material
Die Grundmaterialkosten nehmen eine der zentralen Rollen bei der Preisfindung ein. Dieser Faktor wiegt beim SLS und HP MJF Verfahren wesentlich mehr als beim FDM Verfahren. Wir erklären Ihnen warum das so ist.
Bei den pulverbettbasierten Verfahren muss neben der eigentlichen Bauteil-Materialmenge, auch die Materialmenge betrachtet werden, die zum Auffrischen des Pulvers notwendig ist. Denn dem bereits Hitze ausgesetzem Material muss frisches Pulver hinzugegeben werden, um bei weiteren Druckjobs eine gleichbleibende Qualität sicherstellen zu können. Des weiteren ist die Prozessgeschwindigkeit dieser Verfahren im Gegensatz zum FDM Verfahren wesentlich höher, was wiederum bedeutet, dass die Maschinenkosten pro Bauteil einen kleineren, die Materialkosten jedoch prozentual einen höheren Anteil einnehmen. Das wird insbesondere beim HP MJF Verfahren deutlich. Da bei diesem Verfahren die Prozesszeit jeder Bauteilschicht, unabhängig der Bauteilanzahl oder der Materialmenge, identisch und zudem sehr kurz ist, sind auch die Maschinenkosten auf ein Minimum reduziert. Eine genaue Beschreibung der einzelnen Verfahren finden Sie auf unseren Technologieseiten.
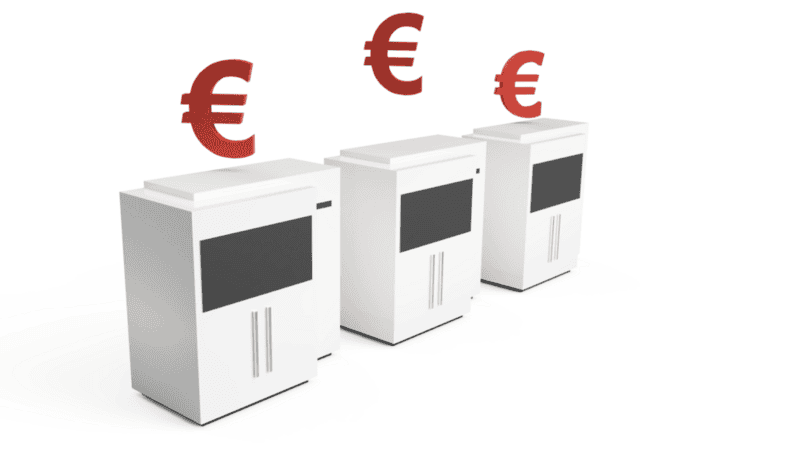
Maschinenkosten
Im Gegensatz zu den Materialkosten ist beim FDM Verfahren der Anteil der Maschinenkosten in der Gesamtkalkulation höher als bei den wesentlich schnelleren pulverbettbasierten Verfahren. Das führt häufig dazu, dass bestimmte, kleinere Bauteilgeometrien in den wesentlich hochwertigeren Verfahren wie bspw. dem selektive Lasersintern (SLS) günstiger sind als im qualitativ schlechteren FDM Verfahren. Diesen Preisunterschied können die günstigeren Materialkosten auch nicht mehr einholen. Die letzte Möglichkeit bieten häufig nur wesentliche gröbere Einstellungen, sodass das FDM Verfahren preislich mit den pulverbettbasierten mithalten kann.
Anders verhält es sich bei großen und voluminösen Bauteilen. Da beim FDM Verfahren mit einer Füllung, auch „Infill“ genannt, gearbeitet wird, welche i.d.R. bei 15-40% liegt, ist auch entsprechend weniger Zeit für den Druck der Füllung notwendig. Dieser Umstand macht das FDM Verfahren bei großen Bauteilen kostentechnisch aktuell unschlagbar.
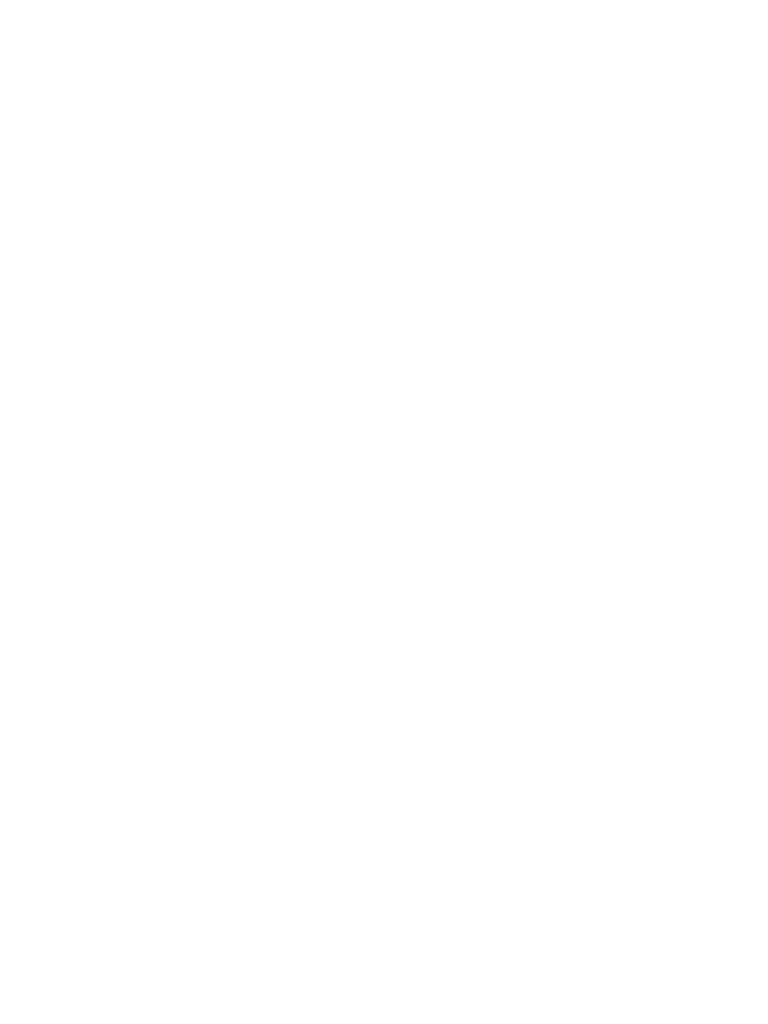
Manuelle Tätigkeiten
Bei jeder verwendeten 3D Druck Technologie und jedem Auftrag entstehen nicht zu unterschätzende manuelle Tätigkeiten. Aus diesem Grund nutzen wir unter anderem auch einen Mindestbestellwert, der den minimal notwendigen Umsatz für eine wirtschaftliche Auftragsbearbeitung abbildet.
Typische vor- und nachgelagerte manuelle Tätigkeiten die einen entscheidenden Einfluss auf die Preisbildung haben, sind:
- Überprüfung der 3D Daten auf Druckbarkeit
- Vorbereitung/Slicing/Packen der Druckjobs
- Vorbereitung der Anlage
- Entnahme/Entpulvern/Finish der Bauteile
- Ggf. Entfernen der Stützstrukturen
- Qualitätsprüfung
Ein Teil der beschriebenen Tätigkeiten sind pro Auftrag nur einmal notwendig bzw. bei jedem weiteren Bauteil zu vernachlässigen. Demenstprechen bleiben die Kosten pro Bauteil bei einer höheren Bestellmenge nicht konstant sondern fallen ab.
Um ein Gefühl der Preise für verschiedene Bauteile, Technologien, Materialien und Stückzahlen zu bekommen, besuchen Sie doch einfach unseren Online 3D Druck Kalkulator. Hier können Sie ihr Bauteil hochladen und erhalten sofort eine Preisauskunft!
Falls Sie kein 3D Modell haben oder Unterstützung beim Verwirklichen eines Projektes benötigen, bieten wir außerdem einen Konstruktionsservice an, welcher die Modelle für Sie erstellen oder für einen 3D Druck optimieren kann. Stellen Sie hierfür einfach eine Anfrage über unser Kontaktformular.